Plastic plating
The term plated plastic is usually applied to plastic parts electrically coated with a layer of shiny cream metal. Plated plastic parts are widely used in cars, equipment and tools.
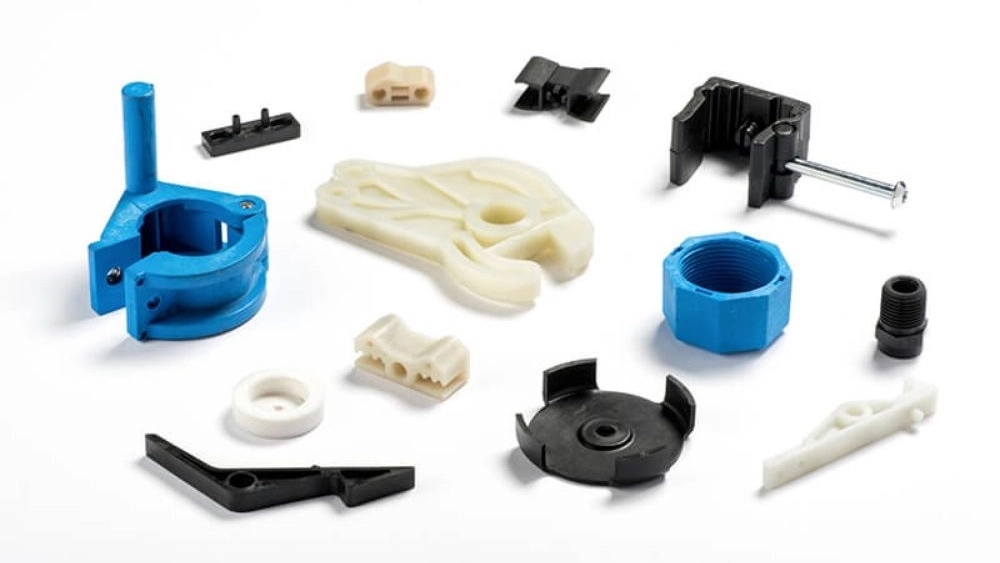
Selection and molding of plastic
Currently, about 85% of the plastic parts that are subjected to the electroplating process are made of acrylonitrile butadiene styrene polymer, which are produced using the injection molding method. In order to achieve a successful electroplating, it is necessary to consider the necessary measures in the design and molding of the plastic part to prevent the appearance of blocked holes, large smooth surfaces and sharp corners. It should be mentioned that during the plastic molding process, it is necessary to observe a series of parameters announced by the designers of the parts, and finally, silicone mold releasers should not be used.
Plating
A typical process for electroplating on acrylonitrile butadiene styrene plastic is shown in figure (1). Of course, other plastics such as polyphenyl oxide, nylon, polysulfone, fluorinated polymers, mixtures of acrylonitrile butadiene styrene and polycarbonate have also been commercially electroplated. Special plating processes for these plastics are provided either by the suppliers of the resins of these plastics or by the suppliers of plating solutions for these plastics. The main difference between these special processes is in the type of solvents, the type of etching solution used, or the type of surface cleaning of plastic parts. The different steps shown in figure (1) can be done in the form of one line or two lines of plating. These plating steps include two parts: the first part during which the plastic part is electrically conductive and the second part where the main metal layer is plated on the plastic part. Of course, in order to improve the quality of work and reduce costs, fully automatic machines are used to perform these steps. It is necessary to pay attention to the fact that it is necessary to use enough water for rinsing at the end of each step.
cleaning
Cleaning of plastic parts, especially when molding and plating plastic parts are done in two different places, requires a separate operation. In the first stage, it should be noted that extreme care should be taken during moving, packing and transporting plastic parts in order to remove pollution such as dust in the air, oils and fingerprints, because some of these pollutions By being absorbed on the surface of the plastic part, they affect the subsequent processes that are done for plating on the plastic part. The purpose of cleaning the plastic parts is to remove the contamination on the surface of the plastic part, which can prevent the chemical attack on the surface of the plastic part in the next step. Alkaline detergents can be mentioned among the most common cleaning solutions.
H Kari
Etching solutions are specially designed to create hydrophobic properties on the surface of the plastic part and produce a finely etched surface that selectively chemically attacks only some of the molecules on this surface. . This micro-etched surface provides the necessary adhesion between the plastic surface and the conductive metal coating that electrifies the plastic surface. Pickling solutions are usually strongly oxidizing solutions that often contain high concentrations of cermic acid and sulfuric acid. Usually, in the case of acrylonitrile butadiene styrene plastic, these etching solutions are used for a period of 10-15 minutes and at a temperature of 60-70 degrees Celsius.
neutralization
Since the presence of hexavalent cream compounds on the surface of the plastic part can be harmful for all subsequent steps in the plating process, often the neutralization step is followed by the use of etching solutions containing cream and in order to remove as much of the compounds as possible. The hexavalent cream transferred from the etching solution is used on the surface of the plastic part. On the other hand, removing the cream salts from the surface of the plastic part helps to better absorb the activator or catalyst in the next step.
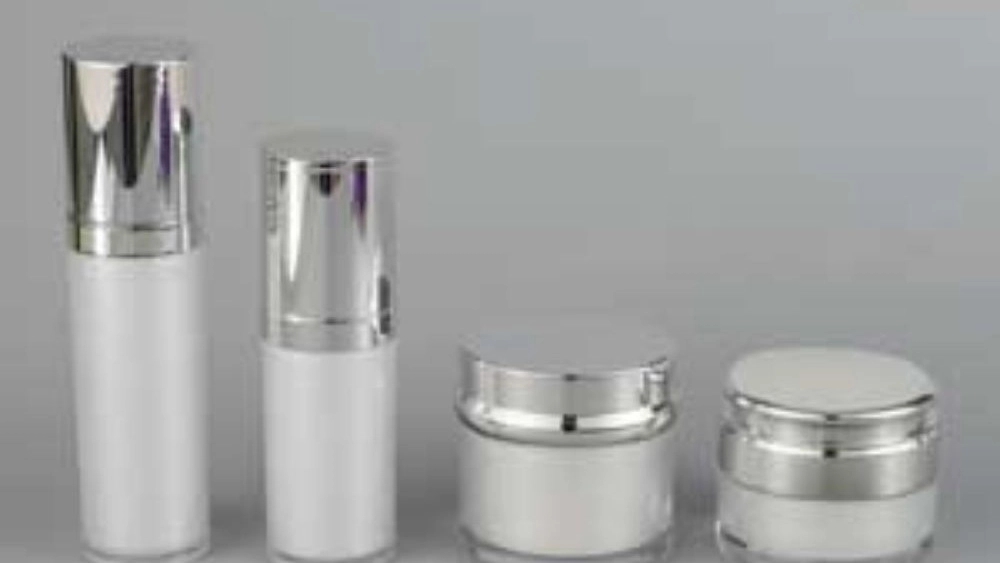
to catalyze
At this stage, in order to start the electroless deposition process, a catalyst is adsorbed on the surface of the plastic piece. Often, the catalyst or activator used in this step is a highly acidic mixture of tin and palladium salts, which is adsorbed to a limited and controllable amount on the surface of the plastic piece. The tin composition in the used catalyst mixture is strongly attached to the surfaces of organic compounds (such as the surface of the plastic piece) and then bonded to the palladium to create a catalytic surface on the surface of the plastic piece. Often, to create a catalytic surface on the surface of the plastic piece, the plastic piece is immersed in a solution of 1-10 percent by volume of the catalyst mixture at a temperature of 15-50 degrees Celsius for a period of 2-10 minutes.< /p>
to speed up
At this stage, an accelerator or post-activator is used to remove excess amounts of tin compounds on the surface of the plastic piece, in order to prevent palladium particles from being covered and exposing them on the surface of the plastic piece. To achieve this goal, place the plastic piece inside for 1-2 minutes
Electroless plating
In the beginning, it is necessary to create a layer of copper or nickel coating on the catalytic surface of the plastic piece electroless (without the use of electric current) in order to electroplate the plastic piece. In most cases, electroless copper plating is used at this stage, due to the existing special external performance considerations. Nickel electroless plating, which has more stable plating solutions, is used in applications where the conditions for using plastic parts will be more severe. Most of the special electroless plating solutions that are used in this step, at room temperature after 5-10 minutes, create a layer of metal coating on the surface of the plastic part that is sufficient to create electrical conductivity. The special electroless plating solutions used in this step are usually extremely stable, so that copper electroless plating solutions are stable and usable for months and nickel electroless plating solutions are stable and usable for more than a year. Since the concentration of the metal coating created on the surface of the piece
The plastic at this stage is about 0.75-0.12 micrometers, it is very important to be very careful in moving and transferring these parts to prevent damage to the metal coating created.
p>
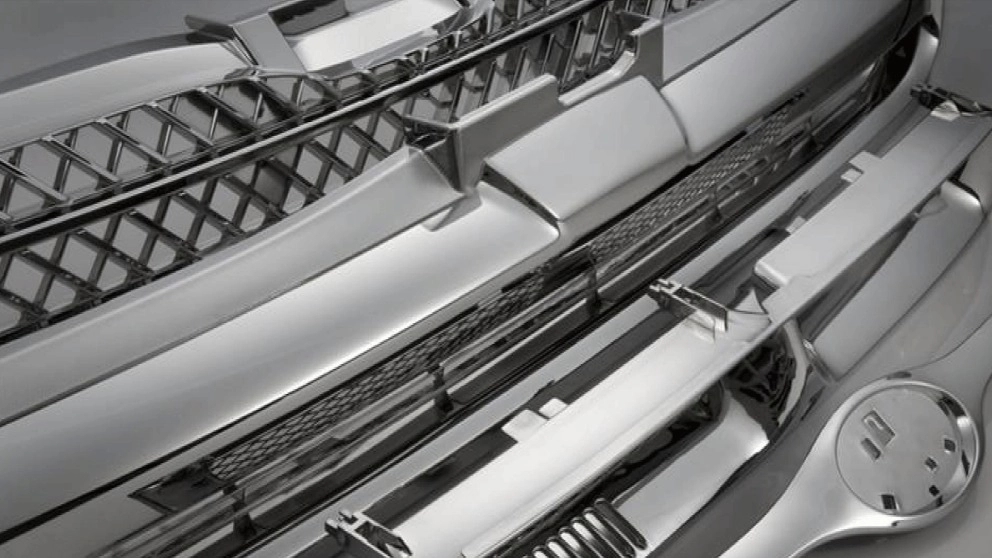
Electric plating
In all the steps mentioned so far, the plastic piece can be hung inside the respective solutions using a hanger, or the plastic piece can be immersed inside the respective solutions using a net and a basket. But at this stage (that is, electroplating), most of the plastic pieces are placed inside the plating solution using plating hangers, and only small parts are immersed in the plating solution using nets. When electroplating hangers are used, it is necessary for the hangers to have strong and electrically strong connections with the plastic part to prevent the plastic part from floating inside the plating solution on the one hand, and on the other hand to provide sufficient electric current to the plastic part. reach the surface of the plastic piece. Although the electrical conductivity of the electroless coating created in the previous step on the plastic piece in the case of small pieces
And the average direction of carrying the electric current required for electroplating on the surface of the plastic part is sufficient, but in the case of large parts such as car parts, the distance between the electroplating hanger and some parts of these parts is large enough to meet the electric current required for electroplating. The electricity that reaches these parts of the piece is not enough. In this case, before starting the main electroplating, create a lining layer of copper or nickel
The use of a high efficiency plating solution at a low current density can be very useful in order to prevent the electroless coating from burning on the plastic part during the main electroplating. The thickness of this lining layer is usually less than 2.5 micrometers. The subsequent glossy, smooth and flexible coating is obtained using an acidic copper sulfate plating solution. This copper coating is created on the one hand to improve the surface appearance of the next coating and on the other hand as a stress absorbing layer that includes both the stress of the next nickel layer placed on it and the stress caused by the difference in thermal expansion of the plastic piece. And the metal layers coated on it are beneficial. The thickness of this copper layer varies depending on the type of design and size of the plastic part and also the purpose of plating the plastic part. For example, the thickness of 15 micrometers is sufficient for handles, as well as TV and radio frames and other small decorative parts. While for larger parts that are supposed to be used in environments with temperature changes, as well as for internal parts. A minimum thickness of 20 micrometers is necessary for this layer. The outer parts of the car, which are large and must withstand many temperature changes, need a thicker copper layer of 0.25-0.20 micrometers. In general, the greater thickness of this copper layer can be used to improve the quality of the final coating. Any other type of metal coating can be used on the acid shiny copper coating. In any case, in order to achieve special characteristics, nickel or cream coatings are commonly used on the copper layer. While in the electroplating of most of the instruments as well as the interior parts of the car, a layer of shiny nickel coating and then a layer of cream coating are used, in the case of the exterior parts of the car, a layer of sulfur-free and semi-glossy nickel coating is used, then a layer of fully shiny nickel coating. And a layer of cream coating with microcracks or microholes is used. Table (1) presents the minimum thickness of the coating created on the plastic piece that can be beneficial in different environmental conditions. These thicknesses have been determined based on investigations on adhesion, corrosion resistance and resistance to temperature changes.